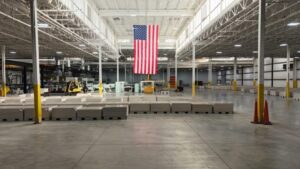
Rigid core flooring like SPC is traditionally an imported product. While its origin has expanded beyond China to include other areas of Asia and Europe, imports have reigned supreme for years. And while that fact may not yet be changing, the influx of domestically produced rigid core is starting to bend the rule.
The atmosphere started to shift around 2019 when the United States Trade Representative (USTR) enacted a 25% tariff on all vinyl flooring made in China. Grumbling continued in 2020 when the decision was made not to include floor covering in the list of items granted exemption from the Section 301 tariff. At the time, the retail community collectively shrugged at the news given the sheer volume of rigid core flooring it was selling.
In early 2023 a new burden was placed on vinyl suppliers and their customers when U.S. Customs began enforcing the Uyghur Forced Labor Protection Act (UFLPA), which was passed into law by the U.S. government in 2022. UFLPA prohibits the importation of all goods that are produced in or contain any content from the Uyghur region in China—an area believed to house forced labor operations and is a major supplier of PVC and raw materials to China and the greater Asian region.
While supplier didn’t begrudge the sharp attention the government brought to unfair and unlawful labor practices, it did force them to acknowledge the vulnerability of their supply chains—especially as it related to vinyl.
Today, there are about 13 domestic producers of vinyl flooring and about eight that specialize in rigid core. That number has steadily grown from just a handful of years ago when it sat at nearly zero.
5 years or less
The rigid core category itself is still young compared to many of its competitors, and so it makes sense to reason that domestic production of these products is young as well. In fact, most of the U.S. factories producing rigid core flooring today are less than 5 years old—most about 3-4, in fact.
For example, Shaw’s rigid core/SPC facility, located in Ringgold, Ga., commenced official production in the fourth quarter of 2020. The facility has undergone updates since its initial opening, with modifications having been made to enhance delivery systems, upgrade extrusion equipment and refine pulverization processes.
“Our domestic production grants us deeper insights into the extraction technologies, enabling us to deliver optimal value and quality,” Doug Morgan, divisional vice president – hard surface, Shaw, told FCNews. “This advantage extends beyond domestic boundaries, benefiting our customers through our network of source partners as well. Furthermore, our local production enhances service reliability and minimizes risks within the supply chain. By ensuring a consistent supply, we mitigate disruptions and provide our customers with the assurance of uninterrupted access to our products.”
Around the same time, Q4 2020, United Surface Solutions’ Chatsworth, Ga., operation—a 400,000-square-foot vertically integrated manufacturing facility located on 150-acres—officially opened. Today the plant is currently in a phase 2 expansion that will bring its capacity to 200M square feet annually. “United Surface Solutions is an American family owned and operated hybrid SPC, service-focused manufacturer offering our customers alternatives to imported SPC/WPC products with our domestic hybrid Composite Rigid Core (CRC) products,” said Nick Brown, vice president of sales. “With the continued challenges and uncertainties with imports, we strive to offer our customers a reliable, proven domestic source, which allows them to go to market with confidence and to build their brands more successfully in the fastest growing segment of the American flooring market.”
The following year, Wellmade completed construction of its 328,000-square-foot, state-of-the-art manufacturing facility in Cartersville, Ga. The company’s exclusive HDPC rigid core products are produced there at a capacity of 100M square feet per year, which is expected to expand to 200 million by September of this year.
“The factory continues to undergo improvements,” Richard Quinlan, senior VP sales and marketing, Wellmade, told FCNews. “For example, in 2023 Wellmade added new equipment to increase production speed and improve overall product quality. New, state-of-the-art production equipment is currently being added as we double production capacity in 2024.”
Quinlan noted that domestic production of rigid core flooring offers the ability for its customers to reduce capital costs associated with inventory produced overseas; provide shorter lead times; eliminate supply chain disruptions and much more. “As global issues continue to add risk and costs to imported vinyl products, Wellmade’s high-quality, made-in-the-USA HDPC-SPC vinyl products offer our customers a safer, lower-risk option compared to imports,” Quinlan said. “We are committed to producing and developing innovative leading-edge designs, delivered efficiently and profitably to our partners throughout the flooring industry.”
Another leader in the space, Novalis Innovative Flooring, also opened its domestic facility in 2021. When the facility first opened in Dalton it was equipped with state-of-the-art machinery and automation technologies. Since then, the company has made some minor changes, mostly with regard to processes and procedures that better position the team for success, according to Kimberly Hill, director of marketing and creative design.
While there are no immediate plans for expansion Novalis said it is continuously looking at future opportunities that would benefit both its customers and overall business. “The most significant benefits for the customer are proximity to our facilities and overall speed to market,” Kimberly Hill, director of marketing and creative design, told FCNews. “Having a domestic presence also gives us more frequent opportunities to show customers what our manufacturing facility and processes look like firsthand, and how those set us apart from our competitors.”
Huali Floors, a China-based manufacturer of resilient flooring, established its first U.S. headquarters and manufacturing facility in 2021 as well. The Chatsworth, Ga., facility has an annual total production capacity of approximately 144 million square feet. Summer Turner, vice president of sales, explained that the building has undergone many structural enhancements and improvements to best support the weight, stability, air quality, water reclamation and overall efficiency throughout the manufacturing process since it first opened. “We are currently expanding our extrusion, coating and profiling capacity by install- ing additional in-line machinery to better service our customers,” she added.
Domestic production, according to Turner, offers Huali’s customers numerous benefits including lower inventory exposure, lower shipping costs and shortened lead times. As well as the fact that new/custom programs can be much faster to launch versus the traditional new program development process when importing.
Made in North America, Mohawk’s Mexicali, Mexico facility opened with true SPC-style machinery in 2022. In 2023, those lines were added to its Dalton facility, which now has the same machinery to produce rigid core flooring. “In addition to the machinery updates, we’ve also continued to bring our technological innovations into our North American facilities,” explained Sarah Duncan, senior product manager, resilient. “For example, our new visual innovation, Signature HDX, will be produced out of our North American facilities in the future.”
Duncan said Mohawk plans to continue to invest in its North American facilities. “With domestic production, we have the ability to produce material when it is needed, without worry of over the water lead times associated with import products,” Duncan noted. “Over the past few years, we’ve seen so many different issues with containers. Overall, domestic manufacturing gives us significantly more control of our supply chain and the ability to get product to our customers when they need it.”
One of the newest kids on the block in rigid core is Engineered Floors, which started 100% production of its PureGrain Direct Digital Print Digital LVT (DLVT) at its Seretean Plant in Dalton in 2023. The company made a large upfront investment to repurpose a section of its Seretean Plant to produce DLVT. The area underwent significant renovations, including raising the ceiling in the extrusion area and upgrades to lighting. EF also has plans to ex- pand its DLVT manufacturing capabilities.
“The peace of mind of our PureGrain DLVT being made in the USA is one of our biggest selling points,” Mike Sanderson, vice president of marketing for Engineered Floors, told FCNews. “We can tell you exactly where all of our raw materials come from. We have complete control of the entire manufacturing process—which happens under one roof—every step of the way. This direct attention gives us unmatched quality control from extrusion all the way to boxing the product.”
AHF Products has one of the most robust domestic production operations as any supplier in the industry. The company currently has seven facilities across the U.S., with 70% of its total volume being domestically produced or sourced products. For rigid core, the company sources from a factory in Georgia. “We have great stateside capacity at a time when domestic supply is important, and world-class manufacturing capabilities that are invigorating our products and the categories we serve,” said Jeff Sommer, director of marketing and digital engagement. “We can maximize our domestic production capabilities and we’re also nimble enough to make timely adjustments in manufacturing and sourcing to address shifting demand. AHF Products is committed to delivering the best products to our customers, which means we will continue to invest in the U.S.”
CFL also provides rigid core flooring via its Calhoun, Ga., facility, which opened in 2022.