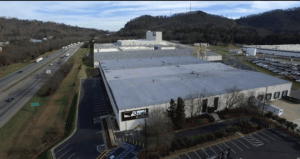
Waterproof features remain a staple in the industry and RSAs continue to tout the performance attribute’s ability to drive customers in-store. What has evolved of late is the expansion of its accessibility. The waterproof label has transcended its rigid core roots and is now touted across a variety of flooring constructions—from SPC to tile and even hardwood and underlayment.
What’s more, much of the production of these waterproof products is happening right here in the U.S. Made-in-America suppliers agree there are a variety of benefits to their customers, not the least of which is shorter lead times—a timely advantage given the hardship imported LVTs continue to face today.
Vinyl, hardwood, laminate
Luxury vinyl flooring and all its iterations remains one of the hottest categories to date with growth outpacing all other categories. As such, manufacturers have seized the opportunity to provide the powerhouse product category with the benefits of domestic production. However, hardwood and laminate can also be found among today’s top domestic waterproof offerings.
One of the most invested suppliers in domestic manufacturing is AHF Products. The company manufactures in eight plants throughout America and produces about 80% of its total volume in the U.S. Domestic products include solid and engineered wood flooring, rigid core (SPC), laminate and accessories.
It produces waterproof genuine hardwood products (Bruce Hydropel; Robbins HydroGuard; and Hartco HydroBlok) at its Somerset, Ky., facility. It manufactures residential sheet, residential and commercial luxury vinyl and VCT at its facilities in Lancaster, Pa., and Kankakee, Ill. Additionally, most of its SPC collections, which also are 100% waterproof, are manufactured domestically in Cartersville, Ga. “Because these products are being made right here in the U.S., dealers and distributors enjoy shorter lead times along with tremendously competitive price points,” said Jennifer Zimmerman, chief commercial officer.
Zimmerman added that the company continues to make investments in its domestic production across the board. “AHF Products is committed to delivering the best products to our customers, which means we will continue to invest in the U.S.”
Mohawk Industries is also heavily invested in its U.S. manufacturing and has facilities in Dalton as well as Mexicali, Mexico, to service its North American customers. The Dalton facility produces waterproof sheet, flex and rigid products while the Mexicali plant—the latest addition to the company’s domestic roster—produces rigid products.
“We are dedicated to domestic manufacturing,” said Adam Ward, vice president, resilient. “The Mexicali plant that we started last year will be completed in 2023, and we continue to add more capacity to our Dalton plant. Both rigid facilities allow us to service the eastern and western regions more efficiently in comparison to our competitors. Together those provide us with the most domestic capacity of any manufacturer in the U.S.”
Ward added that the new issues with port holds due to some issues in China underscores Mohawk’s commitment to domestic manufacturing. “We’re not having any of those issues. We have faster service, better product and distribution.”
Shaw has invested almost $25 million in its Plant RP (resilient manufacturing) in Ringgold, Ga., since 2019—increasing its domestic manufacturing capacity by approximately 50% in that time. This expansion project at Shaw Plant RP is expected to continue throughout 2023. Additionally, Shaw offers water-resistant, domestically made hardwoods from its Shaw Floors brand.
Domestic manufacturing provides many supply chain and operations benefits, according to Steve Sieracki, VP residential hard surface. “Domestic manufacturing allows us to stay close to the customer and lets us keep close tabs on the supply chain. With that being said, increasing consumer interest in domestically produced flooring is, in large part, due to product availability. As 2023 progresses, Shaw will continue to apply the ‘3 Cs’ litmus test for all manufacturing investments—cost, capacity and capability—and then invest accordingly in our domestic and/or contract manufacturing operations to best serve the needs of all of our customers.”
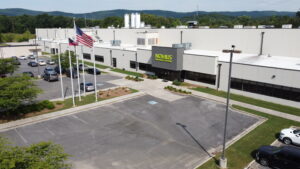
In 2021, Novalis officially opened its Dalton production facility, where it manufactures rigid core LVT products. According to Alyssa Cole, senior content marketing manager, the new facility is equipped with the most advanced technologies in manufacturing and automation. “We are consistently analyzing, innovating and finding new ways to improve our products and processes. This facility allows us to be more closely connected to our customers, servicing their product needs faster while also reducing transportation resource requirements for a more sustainable operation. We are also proud to support a community rich in the history of flooring manufacturing. We strongly feel that this location enables us to attract the best and brightest talent in the industry.”
Cole added that Novalis sees expansion in its future.
Wellmade U.S. operates from a new, state-of-the-art, 328,000-square-foot manufacturing facility located in Cartersville, Ga., which came online at the end of 2021. The new plant is dedicated to the production of Wellmade’s patented HDPC/SPC waterproof vinyl plank. As a new facility, the plant features the latest in flooring manufacturing technology and has quickly ramped up to 130 million square feet of annual production in the first year.
“Our overall goal is to provide stable pricing and readily available stateside inventory while working in tandem with our Chinese manufacturing operations,” said Dick Quinlan, vice president of sales and marketing. “In the end, Wellmade’s goal is to provide a world-class customer experience with improved profits for our partners while producing high-quality, on-trend flooring products to the industry.”
Last year, Mannington continued to onshore additional SKUs of U.S.-produced Adura Max and continued onshoring will continue to occur in 2023, according to David Sheehan, senior vice president, residential product. Adura Flex (Madison, Ga.), Adura Max (Calhoun, Ga.) Restoration Collection (High Point, N.C.), and the original waterproof floor, luxury vinyl sheet (Salem, N.J.), are all examples of Mannington’s domestically produced waterproof floors.
“We’ve transitioned some of our best-selling visuals to U.S.-made Adura Max, and onshoring these visual allows us to provide better service and shorter lead times,” Sheehan explained. “As all [styles] are made here in the USA, retailers are able to enjoy more reliable service, shorter lead times and fewer instances of out of stocks.”
While the bulk of Engineered Floors’ domestic production is in soft surface, the company has recently been investing in the resilient side of the business with the update of its Seretean facility in order to produce domestic LVT in the near future. “Engineered Floor has always seen the value of domestic manufacturing, whether it’s carpet or our future LVT, there is an expectation of exceptional service and quality that consumers have when seeing the Made-in-America label,” said Mike Sanderson, vice president of marketing. “We have made our home in Northwest Georgia for a reason, we support our community and rely on the generations of experience and expertise in the flooring industry to make the most innovative products possible. As a business, we want to limit our exposure to the potential volatility of imported materials, services or products and instill confidence and trust that our retail partners not only have in our products but also in us.”
Nox Corporation, one of the largest global LVT manufacturers, is in the unique position of having its U.S. manufacturing facility in the center of the country—Fostoria, Ohio, to be exact. This provides it with the advantage of more easily servicing both its West and East Coast customers. “Coming out of the pandemic, I think a lot of people had a wake-up call,” said David Thoresen, senior vice president, product and innovation. “People were waiting nine to 10 months to get a container ship out of Asia, and it really helped people realize they need a source for U.S. production. It changed everything. Now the containers are back and the price is falling through the basement but most people who learned the hard way are still leaning on stateside production.”
At its U.S. facility Nox produces loose lay and glue-down LVT. The plant has reached its “sweet spot” in terms of capacity, according to Thoresen, and will continue to operate at a pace best suitable for the needs of its client base across the country.
CFL has a significant presence in SPC and in 2020 brought online what it calls the biggest SPC manufacturing plant in North America, located between Calhoun and Adairsville, Ga. The state of-the-art facility demonstrates CFL’s commitment to delivering high-quality and sustainable flooring solutions to its customers while also supporting the local economy, according to Thomas Baert, founder and president.
Tile
While it may be overlooked due to the enormity of the resilient flooring category, tile has long been touted as a waterproof building material. What’s more, several tile suppliers are producing their wares right here.
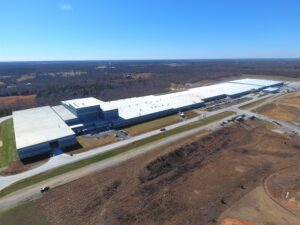
One of the largest tile brands in the world, Daltile operates eight facilities in the U.S.: El Paso, Texas; Fayette, Ala.; Sunnyvale, Texas; Muskogee, Okla.; Dickson, Tenn.; a second Dickson, Tenn., location; Florence, Ala.; and Gettysburg, Pa.
By far the largest U.S. tile producer, Daltile has a total U.S. capacity of over half a billion square feet per year. “Daltile’s domestic production is the solution to the current supply chain issues within the construction and renovation industries,” said Claudio Caselli, senior vice president, product R&D. “The Daltile brand has always had a distinct competitive advantage when it comes to fulfilling the quick-turn demands that have become the norm in the industry, given our vast quantity of made-in-the-USA products. Local production also means we are able to quickly meet changing trends and new style demands. Our customers and end consumers can rely on the trusted quality of U.S. workers. They can also have peace of mind that our manufacturing processes and final products meet the higher environmental and indoor air quality demands that U.S. regulation places on domestically produced goods.”
Slated to open and be fully operational this month, Portobello America’s Baxter, Tenn., manufacturing plant features the latest technology and machinery, which enables it to produce a wide range of products and provide better services to its customers. The plant is designed to reduce waste, improve quality control and increase production capacity to meet the growing demand for U.S.-based manufacturing facilities.
“Our extensive product line will be made here, for here,” said Mike Ward, vice president of sales. “This new facility allows us to deliver total solutions for all customers’ tile needs and positions us for continued growth in the years ahead.”
The new plant will produce a wide range of products, including porcelain tiles, ceramic tiles, polished tiles, in-house trims and mosaics. “Our main goal is to be 100% customer-focused,” Ward noted. “This will include being a leader in product design, total client experience, sustainability and a best-in-class onsite showroom.”
Sundries
Water-resistant sundry suppliers can also tout domestic manufacturing. MP Global, for example, manufactures all of its recycled, fiber-based underlayments in Nebraska. “In the last five years we have reformatted our line and some equipment—over $1 million in capital improvements—to ensure our line is cost efficient and cost competitive in the market and keeps producing high-performance products,” said Deanna Summers, marketing director. “We are great, margin-rich add-ons to the retailer’s bottom line, we offer protection and enhancement to the life of the floor and since we are made in the USA, we have been rock steady in production and supplying our customers quality products throughout the pandemic. We are a one-source underlayment provider—providing shipping efficiencies and harbor all types of industry products.”
Foam Products produces in Calhoun, Ga., and Erwin, Tenn. Its premium moisture blocking flooring underlayment is Eco Silencer Infinity/Max. Foam Products will be adding foam production equipment to handle increase capacity with its current products, in addition to building a new facility to manufacture pre-attached underlayments for the OEM vinyl and laminate manufacturers.
“With continued issues of short supply, increased overseas costs and unsettled political environment with the Chinese manufacturers/government, the domestic products continue to be in the forefront of consumer interest,” said Jim Wink, vice president of sales and marketing. “Domestic production is the key to U.S. independence.”
Future Foam produces foam in five strategically located foam pouring and carpet cushion plants (California, Texas, Wisconsin, Florida and Pennsylvania), as well as 15 fabrication plants—all in the U.S. The company produces its Spillsafe Moisture Barrier in all five of these plants. “We are always updating our equipment and processes for improved safety and proficiency purposes, and three of our five plants had extensive upgrades in the 2022 off season,” said Mark Foster, director of sales. “We spend a lot of time and resources pushing the production bottle neck down the line, which improves output but our target is ‘better’ not so much ‘more.’”
Leggett & Platt produces its hard surface underlayment, Whisper Step, in Cape Girardeau, Mo., and is currently working on a second line to increase capacity. “Being able to ship from a domestic facility allows for shorter lead times and improved quality control,” said Chris Palmer, vice president, sales. “Additionally, we stock the underlayment at all of our rebond facilities.”